PT&P has acquired the metal expansion joint business of RM Engineered Products, Inc. This acquisition included the design software, drawings, business records and all the equipment used to manufacture metal bellows. The equipment was moved from their plant in Ladson, South Carolina and installed in our new building here in Houston. The move and installation efforts were managed by Rick Thompson who joined PT&P in 1995. Rick will be in charge of manufacturing and fabrication of these products.
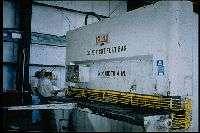
Photo 1
How to Make a Simple Bellows
Photo 2 shows a roll of stainless steel next to a shear which is used to cut the starting piece for the bellows. The particular metal required depends on the temperature, pressure and other design parameters for the expansion joint. Table 1 shows the standard metals used and the corresponding ASTM specification.
Table 1 | |
Material Type | ASTM Material Specification |
304 S/S | A-240 |
304L S/S | A-240 |
316 S/S | A-240 |
316L S/S | A-240 |
321 S/S | A-240 |
Monel 400 | B-127 |
Inconel 600 | B-168 |
Inconel 625 | B-443 |
Incoloy 800/H | B-409 |
Incoloy 825 | B-424 |
Hastelloy C-276 | B-575 |
Rectangular pieces are rolled to form a cylinder with an open seam. The automatic TIG flat bed welding machines shown in Photo 3 require only a few minutes to produce a homogenous weld. Proper set-up of the machine is critical to the quality of the weld. One of the capabilities we have added is an x-ray machine to verify the quality of the welds.
The next step is to shape the required convolutions. Convolutions provide the flexibility required and the total movement capacity of the bellows is proportional to the number of convolutions. The convolutions are formed in two steps. The first step produces a v-shaped circular expansion at the center line of each convolution. The second step extends the triangular shape and provides a flat ring shape for the convolution. This entire process is called roll-forming. Photo 4 shows a roll-forming machine. Different size convolutions require varying set-ups. The arms of a machine for much larger units can be seen in the background.
Bellows are the primary “building blocks” for a variety of expansion joints. The spring rate is determined by the size of the convolutions and the metal used. The compression, extension, lateral offset, rotation etc. required for a particular application determines the design required for the entire expansion joint. Photo 5 shows a “wedding cake” machine used to size bellows when fitting them to other components of the expansion joint.