| FIELD SERVICE
CALL OUR FIELD SERVICE TEAM NOW: +1 (713) 731-0030 | or click here to request assistance from PT&P’s Field Service
On-site Field Services
Pipe Expansion Joint Installation & Maintenance Guide
U.S. Bellows has extensive experience providing on-site services in quick-turn or emergency response situations. U.S. Bellows can provide on-site services for pipe expansion joints (as well as for pipe supports) which include the following:
- Installation guidance
- Inspection and maintenance
- Problem resolution
- Quick-turn expansion joint replacement during shutdowns and turnarounds
U.S. Bellows is also available on a 24 x 7 basis to fulfill any emergency requirements that might arise. We have a system of stock pipe expansion joints as well as an “on-call” engineering and manufacturing team to meet any of your quick-turn and emergency requirements.
Inspection Checklist — Pipe Expansion Joints
- Check for signs of leakage or loss of pressure
- Inspect for any distortion or yielding of anchors, hardware, bellows and piping components
- Observe for any unanticipated movement or piping due to pressure
- Observe for expansion instability (squirm) in the bellows
- Check the pipe or jacket around guides and other moveable parts for evidence of binding
For the quickest response in such an emergency type situation, fill-out the online request form and U.S. Bellows guarantees a response to your request within 30 minutes. Once we receive your request, we will made contact with you and understand the situation, U.S. Bellows will work hard to assist you.
Field Service and Smart Maintenance Solutions
- 40+ Years of Manufacturing & Field Services
- 3 Million+ Pipe Supports Installed
- 1000+ Audits for Pipe Supports & Expansion Joints
- First use of Sensors/AI in Pipe Supports
- 50+ Stress Engineers & Designers
Expertise & Service
- 24×7 Global Support
- 150+ Years Combined Field Experience
- 50+ Design Engineers
- 500+ Production Experts
- Grade A Safety Record
- Knowledge Base of 1000+ Audits
Who We Serve
- All Major Petro-Chemical
- Power Generation
- Food & Industrial Processing
- Semiconductor
- Automotive
- Military & Defense
- Shipping
Competitor Expansion Joints to be Refurbished or Replaced
| FIELD SERVICE
CALL OUR FIELD SERVICE TEAM NOW: +1 (713) 731-0030 | or click here to request assistance from PT&P’s Field Service
On-site Field Services
Pipe Expansion Joint Installation & Maintenance Guide
U.S. Bellows has extensive experience providing on-site services in quick-turn or emergency response situations. U.S. Bellows can provide on-site services for pipe expansion joints (as well as for pipe supports) which include the following:
- Installation guidance
- Inspection and maintenance
- Problem resolution
- Quick-turn expansion joint replacement during shutdowns and turnarounds
U.S. Bellows is also available on a 24 x 7 basis to fulfill any emergency requirements that might arise. We have a system of stock pipe expansion joints as well as an “on-call” engineering and manufacturing team to meet any of your quick-turn and emergency requirements.
Inspection Checklist — Pipe Expansion Joints
- Check for signs of leakage or loss of pressure
- Inspect for any distortion or yielding of anchors, hardware, bellows and piping components
- Observe for any unanticipated movement or piping due to pressure
- Observe for expansion instability (squirm) in the bellows
- Check the pipe or jacket around guides and other moveable parts for evidence of binding
For the quickest response in such an emergency type situation, fill-out the online request form and U.S. Bellows guarantees a response to your request within 30 minutes. Once we receive your request, we will made contact with you and understand the situation, U.S. Bellows will work hard to assist you.
Field Service and Smart Maintenance Solutions
- 40+ Years of Manufacturing & Field Services
- 3 Million+ Pipe Supports Installed
- 1000+ Audits for Pipe Supports & Expansion Joints
- First use of Sensors/AI in Pipe Supports
- 50+ Stress Engineers & Designers
Expertise & Service
- 24×7 Global Support
- 150+ Years Combined Field Experience
- 50+ Design Engineers
- 500+ Production Experts
- Grade A Safety Record
- Knowledge Base of 1000+ Audits
Who We Serve
- All Major Petro-Chemical
- Power Generation
- Food & Industrial Processing
- Semiconductor
- Automotive
- Military & Defense
- Shipping
Competitor Expansion Joints to be Refurbished or Replaced
Read More
When designing specialty pipe supports or expansion joints, we can provide a 3D print that allows our customers to assess the design before it is sent to our shop for manufacturing. Providing our customers with a 3D printed model will help them have a better understanding of the product and its functionality.
3D Big Ton Model
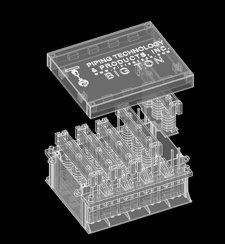
3D Big Ton Model Printed
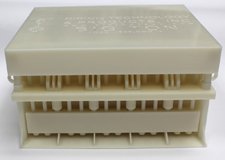
Variable Spring 3D Model
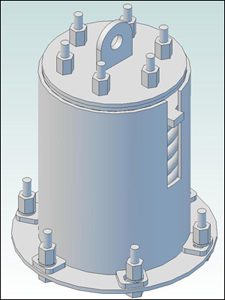
When designing specialty pipe supports or expansion joints, we can provide a 3D print that allows our customers to assess the design before it is sent to our shop for manufacturing. Providing our customers with a 3D printed model will help them have a better understanding of the product and its functionality.
3D Big Ton Model
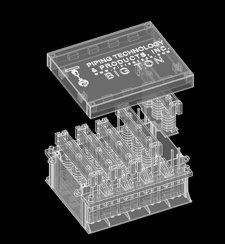
3D Big Ton Model Printed
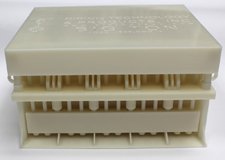
Variable Spring 3D Model
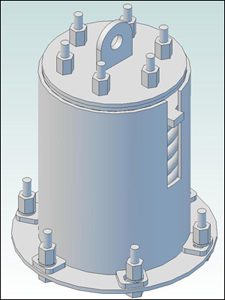
Read More
Pipe Expansion Joint Design & Manufacturing
Engineering and designing is done per EJMA equations as well as per the latest revisions of the ASME B31.3, ASME B31.1, and ASME Section 8, Division 1. U.S. Bellows designs are performed using in-house developed design software and calculations further checked using hand calculations. U.S. Bellows also has full in-house finite element analysis capabilities and we often use this methodology to prove designs.
Manufacturing Capabilities
Metal Forming:
- Hydraulic shears to handle 10 feet of plate up to 1 inch thick mild steel.
- Break presses to handle 14 feet of plate up to ¾” thick mild steel.
- Miscellaneous forming, cutting, and punching machines, including a 50-ton Mubea iron-worker and a 100-ton mechanical.
- Two pyramid plate rollers handle 10 feet of plate up to 5/8 of an inch thick.
- 350-ton radial expander.
- Angle rolling to diameters in excess of 12 feet.
- Plasma cutting up to 2 inches
- Flame cutting 8 torch, computer controlled.
- Horizontal and vertical band saws.
Bellows Forming:
- Roll forming from 24 inches through 15 feet in diameter.
- Expanding mandrel forming from 2 inches through 120 inches in diameter.
- Automatic TIG flat bed welders.
- Bellows reroll and planishing machines.
Machining:
- End Mill. 36 inch travel.
- Bridgeport. Lateral boring to 6 inch diameter and milling with a tilt head on a 36 inch bed.
- Drill presses with 48 inch bed height.
- Surface tables.
- General ability to mill, grind, turn, tap, thread, bore, and chamfer material up to 12 inches in diameter and 36 inches in length.
Quality Control
Additionally, U.S. Bellows does extensive physical testing to prove designs. Each bellows and pipe expansion joint unit goes through in-process quality control controlled using a system of travelers. Final in-house inspection and testing is performed prior to shipping, based on customer requirements. U.S. Bellows has performed a variety of tests on pipe expansion joints ranging from X-Ray tests and hydrotest to helium leak tests (using a mass spectrometer). Our manufacturing shop also has ASME Section VIII CODE certification for jobs requiring CODE certification.
Pipe Expansion Joint Design & Manufacturing
Engineering and designing is done per EJMA equations as well as per the latest revisions of the ASME B31.3, ASME B31.1, and ASME Section 8, Division 1. U.S. Bellows designs are performed using in-house developed design software and calculations further checked using hand calculations. U.S. Bellows also has full in-house finite element analysis capabilities and we often use this methodology to prove designs.
Manufacturing Capabilities
Metal Forming:
- Hydraulic shears to handle 10 feet of plate up to 1 inch thick mild steel.
- Break presses to handle 14 feet of plate up to ¾” thick mild steel.
- Miscellaneous forming, cutting, and punching machines, including a 50-ton Mubea iron-worker and a 100-ton mechanical.
- Two pyramid plate rollers handle 10 feet of plate up to 5/8 of an inch thick.
- 350-ton radial expander.
- Angle rolling to diameters in excess of 12 feet.
- Plasma cutting up to 2 inches
- Flame cutting 8 torch, computer controlled.
- Horizontal and vertical band saws.
Bellows Forming:
- Roll forming from 24 inches through 15 feet in diameter.
- Expanding mandrel forming from 2 inches through 120 inches in diameter.
- Automatic TIG flat bed welders.
- Bellows reroll and planishing machines.
Machining:
- End Mill. 36 inch travel.
- Bridgeport. Lateral boring to 6 inch diameter and milling with a tilt head on a 36 inch bed.
- Drill presses with 48 inch bed height.
- Surface tables.
- General ability to mill, grind, turn, tap, thread, bore, and chamfer material up to 12 inches in diameter and 36 inches in length.
Quality Control
Additionally, U.S. Bellows does extensive physical testing to prove designs. Each bellows and pipe expansion joint unit goes through in-process quality control controlled using a system of travelers. Final in-house inspection and testing is performed prior to shipping, based on customer requirements. U.S. Bellows has performed a variety of tests on pipe expansion joints ranging from X-Ray tests and hydrotest to helium leak tests (using a mass spectrometer). Our manufacturing shop also has ASME Section VIII CODE certification for jobs requiring CODE certification.
Read More
Finite Element Analysis
U.S. Bellows is highly experienced in various design and analysis techniques for piping systems. Given the parameters of your application, U.S. Bellows can use finite element analysis and conventional pipe stress analysis to provide you with an in-depth analysis portfolio that is presentable to your management and your client.
See the photographs below is an example of a gimbal pipe expansion joint fabricated by U.S. Bellows. FEA was used to design the gimbal assembly.
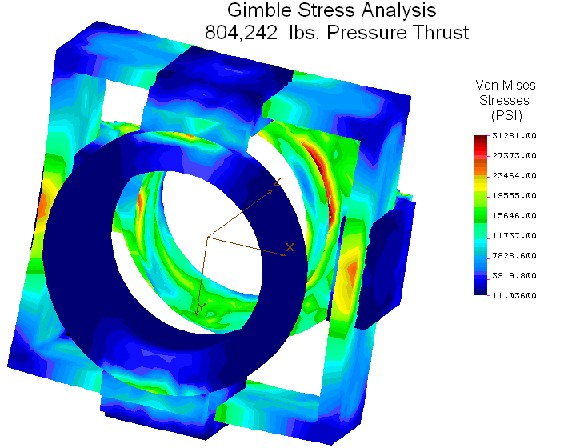
The final product is shown after fabrication completion and then during installation in the plant.
Below is Finite Element Analysis (FEA) on custom designed Tied Universal Pipe Expansion Joint
Finite Element Analysis
U.S. Bellows is highly experienced in various design and analysis techniques for piping systems. Given the parameters of your application, U.S. Bellows can use finite element analysis and conventional pipe stress analysis to provide you with an in-depth analysis portfolio that is presentable to your management and your client.
See the photographs below is an example of a gimbal pipe expansion joint fabricated by U.S. Bellows. FEA was used to design the gimbal assembly.
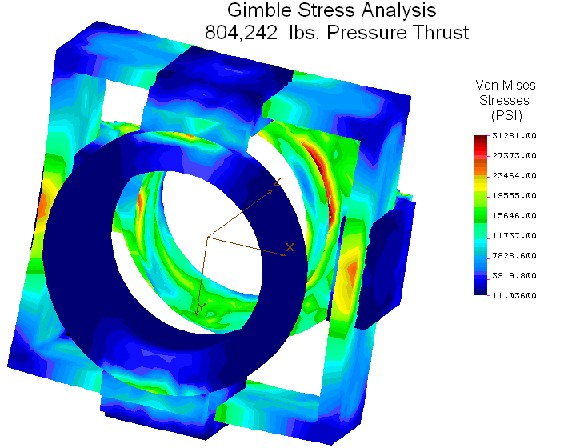
The final product is shown after fabrication completion and then during installation in the plant.
Below is Finite Element Analysis (FEA) on custom designed Tied Universal Pipe Expansion Joint
Read More
Get Immediate Emergency Assistance!
We are here to help you 24 hours a day, 7 days a week.
With a large inventory of stock components for expansion joints and a shop that runs 3 shifts around the clock, U.S. Bellows can quickly assemble and ship products for any situation.
Fill out our emergency service form below and we’ll immediately be notified. A representative will call you back within 30 minutes to assist you. Our response is guaranteed in the evenings and on weekends and holidays.
Emergency Call – Past Experience
An Alaskan petroleum firm called upon the U.S. Bellows Field Service Team on a Friday evening to aid them in an immediate replacement of a defective 48″ diameter pipe expansion joint. The pipe expansion joint was damaged during the plant startup when a G417 pump suddenly failed. A replacement pipe expansion joint was designed, manufactured and shipped the next day. It was installed at the customer’s location within two days of receiving the call.
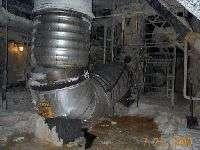 |
|
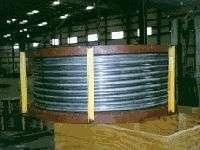 |
|
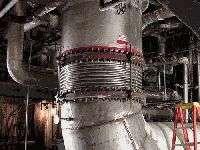 |
Friday, 5:30pm: U.S. Bellows received an emergency call regarding a deformed 48″ pipe expansion joint
|
|
Saturday: The replacement pipe expansion joint is manufactured and ready for shipment.
|
|
Sunday: The new pipe expansion joint is installed on-site.
|
How it Works:
- Submit the form below
- Our “On-Call” Team is immediately paged
- You will be contacted within 30 Minutes
- Fill Out Form Below & Hear from Us Within 30 minutes.
Get Immediate Emergency Assistance!
We are here to help you 24 hours a day, 7 days a week.
With a large inventory of stock components for expansion joints and a shop that runs 3 shifts around the clock, U.S. Bellows can quickly assemble and ship products for any situation.
Fill out our emergency service form below and we’ll immediately be notified. A representative will call you back within 30 minutes to assist you. Our response is guaranteed in the evenings and on weekends and holidays.
Emergency Call – Past Experience
An Alaskan petroleum firm called upon the U.S. Bellows Field Service Team on a Friday evening to aid them in an immediate replacement of a defective 48″ diameter pipe expansion joint. The pipe expansion joint was damaged during the plant startup when a G417 pump suddenly failed. A replacement pipe expansion joint was designed, manufactured and shipped the next day. It was installed at the customer’s location within two days of receiving the call.
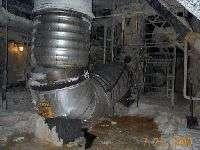 |
|
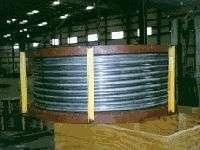 |
|
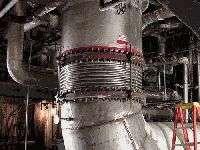 |
Friday, 5:30pm: U.S. Bellows received an emergency call regarding a deformed 48″ pipe expansion joint
|
|
Saturday: The replacement pipe expansion joint is manufactured and ready for shipment.
|
|
Sunday: The new pipe expansion joint is installed on-site.
|
How it Works:
- Submit the form below
- Our “On-Call” Team is immediately paged
- You will be contacted within 30 Minutes
- Fill Out Form Below & Hear from Us Within 30 minutes.
Read More
Expansion Joint Product Testing: Hydro-Testing
Objective: The objective of this test is to check for leakage or cracks in the welding.
What We Do: The bellows is completely filled with a liquid such as water. Pressure is slowly applied to the liquid until the required pressure is reached. This pressure is held for at least 30 minutes at which point the component is inspected visually to locate leaks.
Completion: If a leak is present, the welds will be repaired after releasing the hydro test pressure.
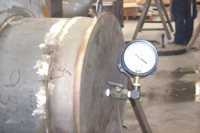 |
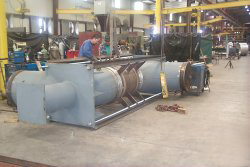 |
Bellows are pressurized |
Pressure is observed |
Expansion Joint Product Testing: Hydro-Testing
Objective: The objective of this test is to check for leakage or cracks in the welding.
What We Do: The bellows is completely filled with a liquid such as water. Pressure is slowly applied to the liquid until the required pressure is reached. This pressure is held for at least 30 minutes at which point the component is inspected visually to locate leaks.
Completion: If a leak is present, the welds will be repaired after releasing the hydro test pressure.
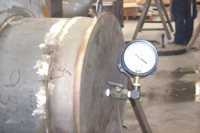 |
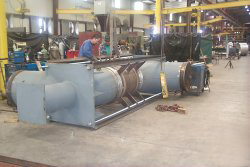 |
Bellows are pressurized |
Pressure is observed |
Read More
Expansion Joing Product Testing: Dye Penetration Testing
Objective: This test is performed to insure there are no weld defects such as surface cracking or weld discontinuities before and after forming the bellows.
What We Do: The weld surface is thoroughly cleaned and a red penetrant dye is applied to the surface of the weld and allowed to soak for a period of time. The dye is then removed and a white powder is sprayed on the weld surface that performs a blotting action.
After Completion: An indication of the dye with a white background characterizes the weld surface discontinuities of the bellows longitudinal seam weld. This testing before and after the bellows forming process ensures a sound quality bellows seam weld.
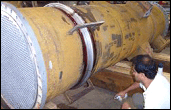 |
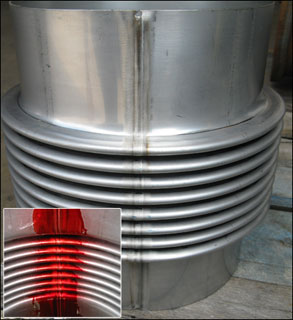 |
Expansion Joing Product Testing: Dye Penetration Testing
Objective: This test is performed to insure there are no weld defects such as surface cracking or weld discontinuities before and after forming the bellows.
What We Do: The weld surface is thoroughly cleaned and a red penetrant dye is applied to the surface of the weld and allowed to soak for a period of time. The dye is then removed and a white powder is sprayed on the weld surface that performs a blotting action.
After Completion: An indication of the dye with a white background characterizes the weld surface discontinuities of the bellows longitudinal seam weld. This testing before and after the bellows forming process ensures a sound quality bellows seam weld.
Read More
Expansion Joint Product Testing: Fatigue Testing
Objective: The objective of the fatigue testing is essentially to verify how many cycles a bellows can withstand before failing.
What we do: The bellows is placed on the “cycle-test machine” and bolted to a hydraulic plunger. Each cycle is counted as the bellows is compressed and returned to neutral.
Fatigue Testing / Cycle Testing Video
This video shows an expansion joint bellows being subjected to a cycle test as required by the customer. The expansion joint is compressed and expanded through its specified design movement of 1 and 1/4 inches to verify the calculated lifespan of 30,000 cycles. The number of completed cycles is recorded throughout the duration of the test.
Expansion Joint Product Testing: Fatigue Testing
Objective: The objective of the fatigue testing is essentially to verify how many cycles a bellows can withstand before failing.
What we do: The bellows is placed on the “cycle-test machine” and bolted to a hydraulic plunger. Each cycle is counted as the bellows is compressed and returned to neutral.
Fatigue Testing / Cycle Testing Video
This video shows an expansion joint bellows being subjected to a cycle test as required by the customer. The expansion joint is compressed and expanded through its specified design movement of 1 and 1/4 inches to verify the calculated lifespan of 30,000 cycles. The number of completed cycles is recorded throughout the duration of the test.
Read More
Stock Metallic Bellows
U.S. Bellows has an inventory of over 1500 stock bellows for your quick-turn/emergency requirements. Using our inventory, we can quickly assemble and ship a variety of expansion joints including single, single tied, universal, elbow pressure balanced and in-line pressure balanced expansion joints. Stock bellows are available from 2″ to 24″ diameter and in three pressure values:
Pipe Expansion Joint Product Testing
U.S. Bellows, Inc. does extensive physical testing ranging from X-Ray tests and Hydrotests to Helium Leak tests (using a mass spectrometer.) Each bellows and pipe expansion joint unit goes through in-process quality control using a system of travelers. Final in-house inspection and testing are performed prior to shipping. Our manufacturing shop also has ASME Section VIII CODE certification.
Fatigue testing is essentially verifying how many cycles a bellows can withstand before failing. The bellows is placed on the “cycle-test machine” and bolted to a hydraulic plunger. Each cycle is counted as the bellows is compressed and returned to neutral.
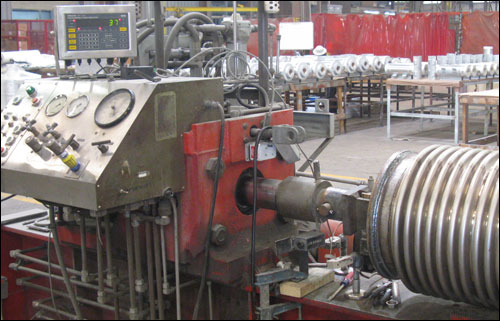
View a Fatigue Test Verifying a Cycle Life of 30,000 (VIDEO)
The objective of the burst test is to determine the ultimate pressure resistance, primarily conducted on bellows. Normally, hydraulic pressure is slowly increased until failure occurs. Pressure balanced pipe expansion joints are designed to maintain a constant volume through the use of a compensating bellows.
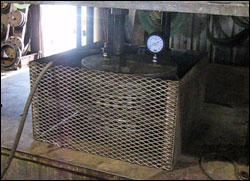
Liquid dye and a white powder observant are used to locate leaks or cracks in the bellows attachment welds. This test is performed for long seam welds before and after forming the bellows.
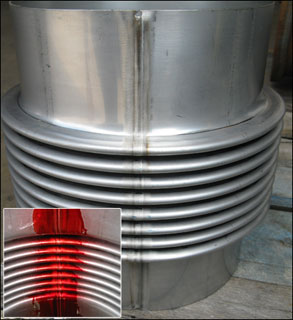
During a hydro-test, the bellows is completely filled with liquid until a desired pressure is reached. The bellows is pressurized for 30 minutes to locate leaks or cracks in the welding.
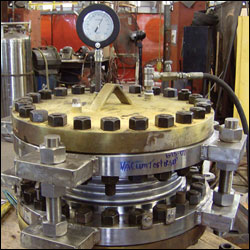
The bellows is filled with pressurized helium and then “sniffed” to detect leaks indicated by a mass spectrometer.
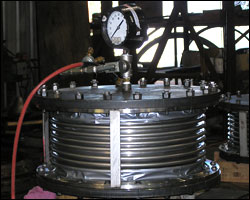
Additional Product Testing:
- Ultrasonic Testing
- Radiography Testing
- PMI Testing
- Pneumatic Testing
- Magnet Particle Testing
Pipe Expansion Joint Product Testing
U.S. Bellows, Inc. does extensive physical testing ranging from X-Ray tests and Hydrotests to Helium Leak tests (using a mass spectrometer.) Each bellows and pipe expansion joint unit goes through in-process quality control using a system of travelers. Final in-house inspection and testing are performed prior to shipping. Our manufacturing shop also has ASME Section VIII CODE certification.
Fatigue testing is essentially verifying how many cycles a bellows can withstand before failing. The bellows is placed on the “cycle-test machine” and bolted to a hydraulic plunger. Each cycle is counted as the bellows is compressed and returned to neutral.
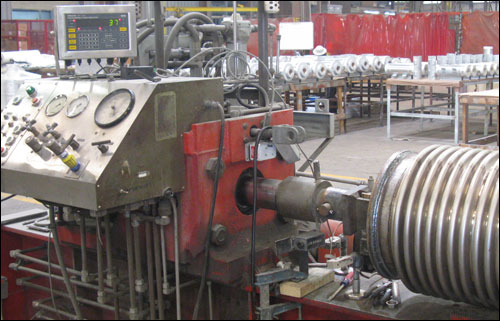
View a Fatigue Test Verifying a Cycle Life of 30,000 (VIDEO)
The objective of the burst test is to determine the ultimate pressure resistance, primarily conducted on bellows. Normally, hydraulic pressure is slowly increased until failure occurs. Pressure balanced pipe expansion joints are designed to maintain a constant volume through the use of a compensating bellows.
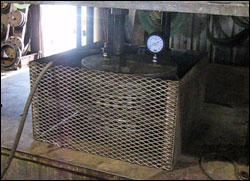
Liquid dye and a white powder observant are used to locate leaks or cracks in the bellows attachment welds. This test is performed for long seam welds before and after forming the bellows.
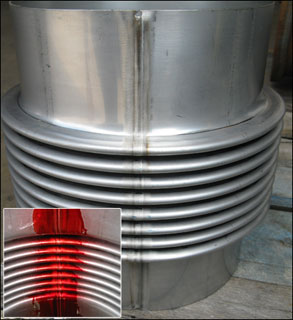
During a hydro-test, the bellows is completely filled with liquid until a desired pressure is reached. The bellows is pressurized for 30 minutes to locate leaks or cracks in the welding.
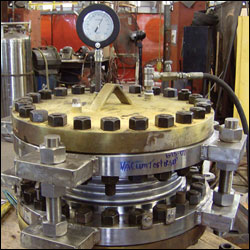
The bellows is filled with pressurized helium and then “sniffed” to detect leaks indicated by a mass spectrometer.
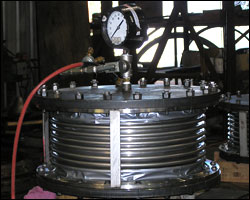
Additional Product Testing:
- Ultrasonic Testing
- Radiography Testing
- PMI Testing
- Pneumatic Testing
- Magnet Particle Testing
Read More
Expansion Joint Product Testing: Helium Leak Testing
Objective: The objective of the helium test is to locate and calibrate leaks.
What We Do: The unit is filled with pressurized helium and the outside is “sniffed” to detect leaks which are indicated by a mass spectrometer.
After Completion: Once the test is completed, leak areas can be passed, rejected or repaired.
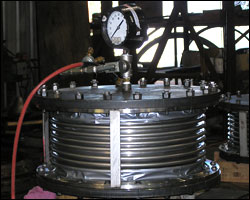
Helium Leak Test Being Performed on an 18″ Diameter Stainless Steel Single Expansion Joint
Expansion Joint Product Testing: Helium Leak Testing
Objective: The objective of the helium test is to locate and calibrate leaks.
What We Do: The unit is filled with pressurized helium and the outside is “sniffed” to detect leaks which are indicated by a mass spectrometer.
After Completion: Once the test is completed, leak areas can be passed, rejected or repaired.
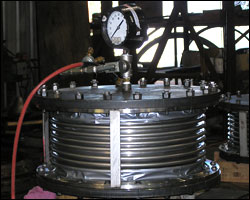
Helium Leak Test Being Performed on an 18″ Diameter Stainless Steel Single Expansion Joint
Read More
Expansion Joint Product Testing: Burst Testing
Objective: The objective of the burst test is to determine the ultimate pressure resistance that a bellows can absorb prior to failure. Burst tests help determine the margin of safety and safety factor to be used in a specialized bellows design.
What We Do: During a burst test, hydrostatic pressure is slowly increased until failure occurs, which usually happens in one to two hours. Burst testing is conducted at ambient temperatures to determine a bellows pressure rating. We follow all the necessary safety precautions for personnel involved, such as placing the bellows in a high strength steel cage and using a safety shut-off switch.
After Completion: Based on the burst test results, a safety factor is applied, thus establishing the ultimate pressure rating.
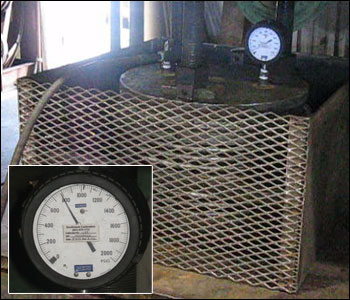 |
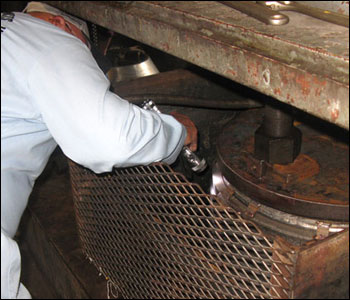 |
Burst Test to 800 psig on a 304 Stainless Steel Bellows |
Q.C. Inspecting the Bellows After a Burst Test |
Expansion Joint Product Testing: Burst Testing
Objective: The objective of the burst test is to determine the ultimate pressure resistance that a bellows can absorb prior to failure. Burst tests help determine the margin of safety and safety factor to be used in a specialized bellows design.
What We Do: During a burst test, hydrostatic pressure is slowly increased until failure occurs, which usually happens in one to two hours. Burst testing is conducted at ambient temperatures to determine a bellows pressure rating. We follow all the necessary safety precautions for personnel involved, such as placing the bellows in a high strength steel cage and using a safety shut-off switch.
After Completion: Based on the burst test results, a safety factor is applied, thus establishing the ultimate pressure rating.
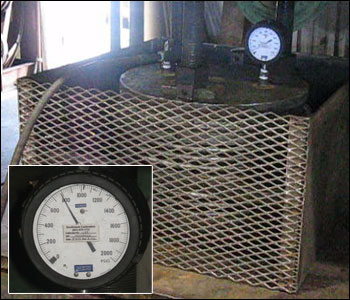 |
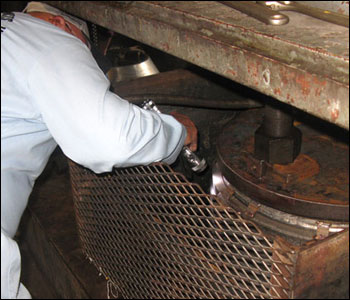 |
Burst Test to 800 psig on a 304 Stainless Steel Bellows |
Q.C. Inspecting the Bellows After a Burst Test |
Read More