The increase in the breach opening along the axis of the duct. In certain configurations, the duct thermal expansion may result in extension at the expansion joint location.
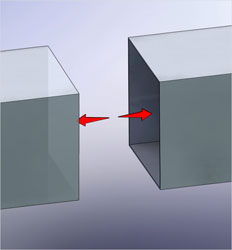
The increase in the breach opening along the axis of the duct. In certain configurations, the duct thermal expansion may result in extension at the expansion joint location.
The increase in the breach opening along the axis of the duct. In certain configurations, the duct thermal expansion may result in extension at the expansion joint location.
It is the opening in the duct where the expansion joint is installed.
It is the opening in the duct where the expansion joint is installed.
The reduction in the breach opening along the axis of the duct. This is usually a result of thermal expansion of the ducting.
The reduction in the breach opening along the axis of the duct. This is usually a result of thermal expansion of the ducting.
It is a structural angle or channel that is welded to the end of the ducting facilitate bolting or welding the expansion joint into the system.
It is a structural angle or channel that is welded to the end of the ducting facilitate bolting or welding the expansion joint into the system.
The rubber molded expansion joint would be used for water services or applications with low temperature.
The rubber molded expansion joint would be used for water services or applications with low temperature.
The installed length is the overall face-to-face length of the expansion joint to be installed.
The installed length is the overall face-to-face length of the expansion joint to be installed.What does installed length refer to in a fabric expansion joint?
We can also do fabric expansion joints but that would be for a very low-pressure application.
We can also do fabric expansion joints but that would be for a very low-pressure application.
The fabric is comprised of various layers:
The fabric is comprised of various layers:What fabric is used in manufacturing expansion joints?
The fabric joints do not have stiffness values as the metallic bellows do.
The fabric joints do not have stiffness values as the metallic bellows do.
Fabric Expansion JointThe maximum pressure for fabric expansion joints is 100 inches of water or 3 PSIG. (pounds per square inch)
Fabric Expansion JointThe maximum pressure for fabric expansion joints is 100 inches of water or 3 PSIG. (pounds per square inch)
These expansion joints are not a good solution for high-temperature applications. The neoprene tends to burn at approximately 250 deg. F.
These expansion joints are not a good solution for high-temperature applications. The neoprene tends to burn at approximately 250 deg. F.
The number of layers or plies is dependent upon the design conditions and we usually limit non-metallic expansion joints to two or three layers.
The number of layers or plies is dependent upon the design conditions and we usually limit non-metallic expansion joints to two or three layers.
We do manufacture fabric expansion joints with other types of materials if the customer specifies it. Please see some of the materials here:
We do manufacture fabric expansion joints with other types of materials if the customer specifies it. Please see some of the materials here:
Read MoreYes, the rubber expansion joints do have spring rates and that are required to be input into the stress model.
Yes, the rubber expansion joints do have spring rates and that are required to be input into the stress model.