Expansion joints failure is caused by corrosion, erosion, cyclic fatigue or thermal creep at elevated temperatures.
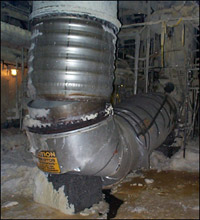
Expansion joints failure is caused by corrosion, erosion, cyclic fatigue or thermal creep at elevated temperatures.
Rubber bellows can crack if they are over-pressurized or placed in a harsh environment.
Rubber bellows can crack if they are over-pressurized or placed in a harsh environment.
Failures can occur for many reasons, but experience has shown that certain causes of failure fall into fairly distinct categories.
Shipping and handling damage. Examples: Denting or gouging of bellows from being struck by hard objects (tools, chain falls, forklifts, adjacent structures, etc.); improper stacking for shipping or storage; insufficient protection from weather or other adverse environmental conditions.
Improper installation and insufficient protection.
During and after installation.
Examples: Joints with internal liners installed in the reverse direction with respect to flow; installing an expansion joint in a location other than as prescribed by the installation drawings; premature removal of shipping devices; springing of bellows to make up for piping misalignment; insufficient protection from mechanical damage due to work in the surrounding area; insufficient protection of bellows during nearby welding operations and failure to remove shipping devices before placing system in operation.
Improper anchoring, guiding and supporting of the system.
Anchor failure in service.
Bellows corrosion, both internal and external.
System over-pressure (in-service or hydrotest). Bellows vibration (mechanical or flow-induced resulting in high cycle fatigue).
Excessive bellows deflection (axial, lateral, angular deflections greater than design values).
Torsion.
Bellows erosion.
Failures can occur for many reasons, but experience has shown that certain causes of failure fall into fairly distinct categories.
Shipping and handling damage. Examples: Denting or gouging of bellows from being struck by hard objects (tools, chain falls, forklifts, adjacent structures, etc.); improper stacking for shipping or storage; insufficient protection from weather or other adverse environmental conditions.
Improper installation and insufficient protection.
During and after installation.
Examples: Joints with internal liners installed in the reverse direction with respect to flow; installing an expansion joint in a location other than as prescribed by the installation drawings; premature removal of shipping devices; springing of bellows to make up for piping misalignment; insufficient protection from mechanical damage due to work in the surrounding area; insufficient protection of bellows during nearby welding operations and failure to remove shipping devices before placing system in operation.
Improper anchoring, guiding and supporting of the system.
Anchor failure in service.
Bellows corrosion, both internal and external.
System over-pressure (in-service or hydrotest). Bellows vibration (mechanical or flow-induced resulting in high cycle fatigue).
Excessive bellows deflection (axial, lateral, angular deflections greater than design values).
Torsion.
Bellows erosion.
The failure mode of bellows could be any of a variety of things including erosion, corrosion, cyclic fatigue or thermal creep at elevated temperatures.
The failure mode of bellows could be any of a variety of things including erosion, corrosion, cyclic fatigue or thermal creep at elevated temperatures.