stress-analysis-faq
Excessive flexibility increases material costs, increases pressure drops, increase vibration, and creates 2-phase flow occurrences.
Increase in the number of segments (nodes) reviewed though computer use and use of precise calculations.
Welds, fittings, branch connections , and other piping components where the possibility of fatigue failure could occur.
The Stress-Intensification Factor is the ratio of the maximum stress intensity compared to the nominal stress.
The maximum shear stress theory states that failure of a piping component occurs when the maximum shear stress exceeds the shear stress at the yield point in a tensile test.
The Maximum Principle Stress Theory and Maximum Shear Stress Theory
This theory states that yielding in a piping component occurs when the magnitude of any of the three mutually perpendicular principal stresses exceeds the yield strength of the material.
Failure by general yielding, yielding at sub-elevated temperature, brittle fractures, and fatigue.
Stress analysis ensures the safety of piping and piping components, safety of connected equipment and supporting structure, and that piping deflections are within limits.
A term applied to calculations, which address the static and dynamic loading, resulting from the effects of gravity, temperature changes, internal pressures, fluid flow, seismic activity, and any external loads.
It is a visual representation of the effects of various loading conditions on a piping system between stress and strain.
Vibration, thermal bowing, creep, thermal fatigue, and steam/water.
Excessive flexibility causes an increase in material costs, pressure drops, and loss of pump efficiency.
Using flexible piping with bends and turns, use of expansion loops between fixed locations, or use of expansion joints between two anchor points of a pipe run.
Flexibility analysis assures that there is not any overstress or fatigue, leakage at joints or distortions are piping connections or terminals.
To produce neither excessive stress within the configuration and limit excessive end reaction at the piping terminal.
Hydro-test pressure and holding times vary for different design codes. For example, the ASME SEC VIII Div.1 general hydro-test pressure will be1.3 x design pressure (minor factors may vary for this equation as well) and for piping design codes, the hydro-test pressure will be ASME B31.4,B31.8 1.5 xdesign pressure.
Usually it would show a disparity between stresses at a particular point. For example, a carbon steel element joined to a stainless steel element would show significantly different stresses over the same temperature change.
Anchors will restrict movement in all directions and will also restrict the rotation of the pipe as well. In the stress analysis, we may see loads in all three directions which will tell us how “strong” the anchor device has to be.
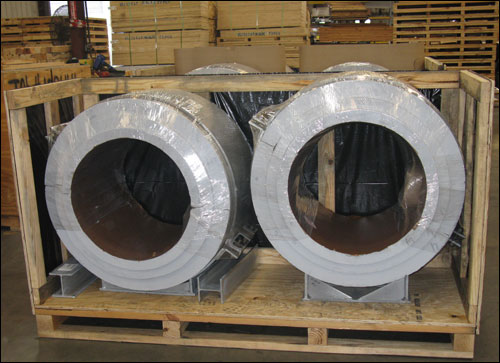
Thermal bowing is the bending of pipe caused by thermal expansion.
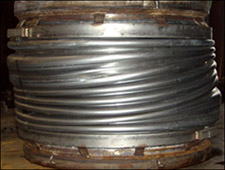
Creep is the tendency of a solid material to move slowly order form permanently under the influence of stress.
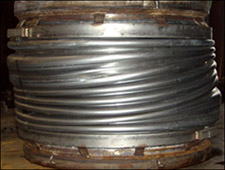
The maximum force (allowable load) is based upon the yield strength of the material with a safety factor. If your calculated load is greater than the maximum force load, then you are abov ethe allowable load and you will start to see deformation and movement that should not be there.
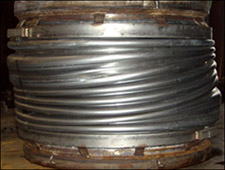
The thermal analysis is done at the design temperature because you aredesigning the system for its most extreme case, where the temperatures are the hottest and the movements are the greatest.
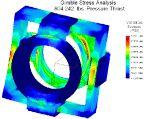
Flexibility ensures that a piping system operates safely.